Belt Fabrication
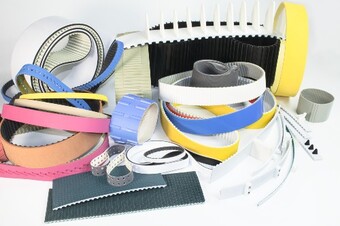
Product Handling belts differ widely in look, material, and size. The most appropriate belt for your application depends on the operating environment and the unique details of the application. Taking the time to understand the product handling environment is key to ensuring optimal performance and longevity.
Megadyne’s expertise is manufacturing rubber and urethane engineered belts for product handling applications. This document will explore the factors influencing belt selection and design, helping to inform our readers and customers during the sourcing process to ensure they select the most appropriate belt for their equipment.
Fabrication Capabilities
Megadyne offers a full range of industrial belts, including timing belts, flat belts, V-belts and multi-rib belts. Within each of these categories, we offer a range of material options and customization possibilities.
Belt Types and Substrates
Product Handling belts can be made from a variety of materials. The most appropriate substrate
depends on the details of the application environment, the type of belt, and requirements for
factors such as stability, flexibility, and service life. At Megadyne, we offer belts made with
urethane or rubber. We can also accommodate special requests with our broad range of elastomer
and reinforcement choices.
- Timing belts
Timing belts are used when synchronized movement or bi-directional conveying is necessary. Urethane and rubber are our most popular elastomer options for these belts. Choice of the right material is highly related to the application environment. Megadyne offers a wide range of reinforcement options, like steel and Kevlar® and variations like high strength and high flex options.
- Flat belts
Flat belts are general-purpose belts used in product handling and power transmission applications. Megadyne’s specialty flat belts are available in a variety of elastomers to suit specific needs, including thermoplastic polyurethane, thermoset polyurethane, silicone rubber, and neoprene. These materials may be reinforced with steel, polyester, nylon, or Kevlar®, and we can provide covers where necessary. Our team will work with you to identify the ideal combination of base and reinforcement materials for your application.
- Multi-rib belts
Multi-rib belts, including multi-rib v-belts, are y made from sturdy polybutadiene elastomer another rubber with favorable wear resistance properties or thermoset urethane. Multi-rib belts offer enhanced tracking ability and greater frictional drive compared to standard flat belts.
Belt Covers and Coatings
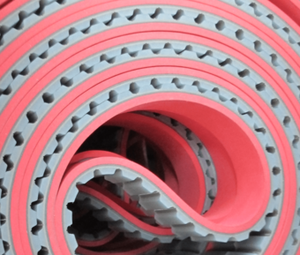
Covers, designed to provide friction or environmental benefits, can be added to any of the Megadyne substrates mentioned above. We offer processes that include molding, lamination, casting and coating.
For example, we might apply a soft foam cover to cushion products during transit to facilitate fragile product handling. Other considerations that might call for a custom cover or coating may include:
- High or low friction requirements
- Transport of abrasive materials
- Exposure to high levels of heat
- Exposure to the elements
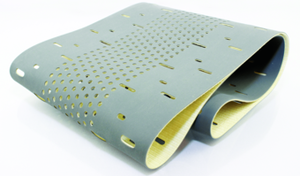
Covers may be smooth or contain surface features that provide grip, temperature resistance, compression, wear resistance or easy release features.
Custom Belt Modifications
Customizations are an important factor for many applications: selecting the correct modifications and a suitable base can be key to lasting performance. Ask your Megadyne belting specialist which modifications can optimize your application.
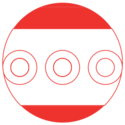
Punching and Perforating
With highly automated CNC equipment, software can be created to deliver precision spaced holes with very close tolerances. Perforated belts generate a degree of suction that holds products more firmly in place. Additionally, perforations are also beneficial where water drainage is essential.
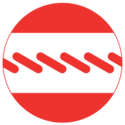
Countersinking, Slotting, and Routing
Countersinking builds up a conical shape around perforations to enhance airflow and increase the suction effect. Slotting and Routing are used to increase the suction area and create a stronger vacuum. Slotting and Routing can also be used to create pockets for holding product in place.
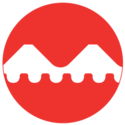
Siping and Grooving
Sipes are created by slitting the belt to relieve stress. Siping is a common protective measure to prevent cracking in thick belts. Siping also prevents dust accumulation. Grooving is similar to siping but produces larger slits that allow water drainage or venting.
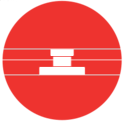
Milling and Grinding
Milling and Grinding are more complicated modifications that require the use of advanced, multi- axle CNC machines. Although these processes require more design and set-up work, they enable a much higher degree of precision and customization, including custom textures, finishes, and tracking designs.
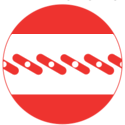
Multiple Modifications
In some cases, multiple modifications may be needed to achieve desired results.
Cleats for Belts
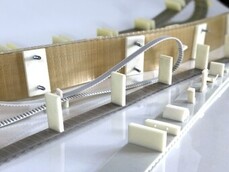
Cleats are often required to stabilize or separate products. This might be necessary to hold products in place during transport or to align them in a specific configuration, such as for indexing. Cleats can be welded onto Megadyne thermoplastic timing or flat belts. Furthermore, cleats can be attached mechanically making removal possible and repositioning easy. Megadyne offers CNC or custom-molded cleats to your exact specifications.
Alternatives to Molding, Laminating and Coating: Spin Cast Technology
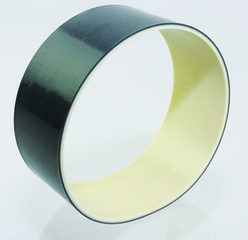
Spin casting is a molding method that delivers precise dimensional features. Using thermoplastic or thermoset elastomers and in-house machined molds we can case single, dual and tri-layer finishes.
To create spin-cast products, we inject raw material into a heated, rotating mold, which produces centrifugal force as it turns. This rotational force holds the raw elastomer against the wall of the mold as it cures, resulting in a smooth and exact surface finish. The wall of our mold can be smooth or contain surface features.
Megadyne uses an advanced computer formula to calculate the exact quantities of raw material necessary for the desired hardness, thickness, and color – ensuring consistent, satisfactory results.
Megadyne Custom Belts and Components
Megadyne is a trusted provider of Engineered belts, having spent 60 years providing custom solutions to customers in a variety of industries. Our professional team will work with you to explore our vast selection of materials and finishes, as well as determine any custom modifications that might improve your results. To begin the process, get in touch with us today.