MEGASYNC™ Titanium
Overview
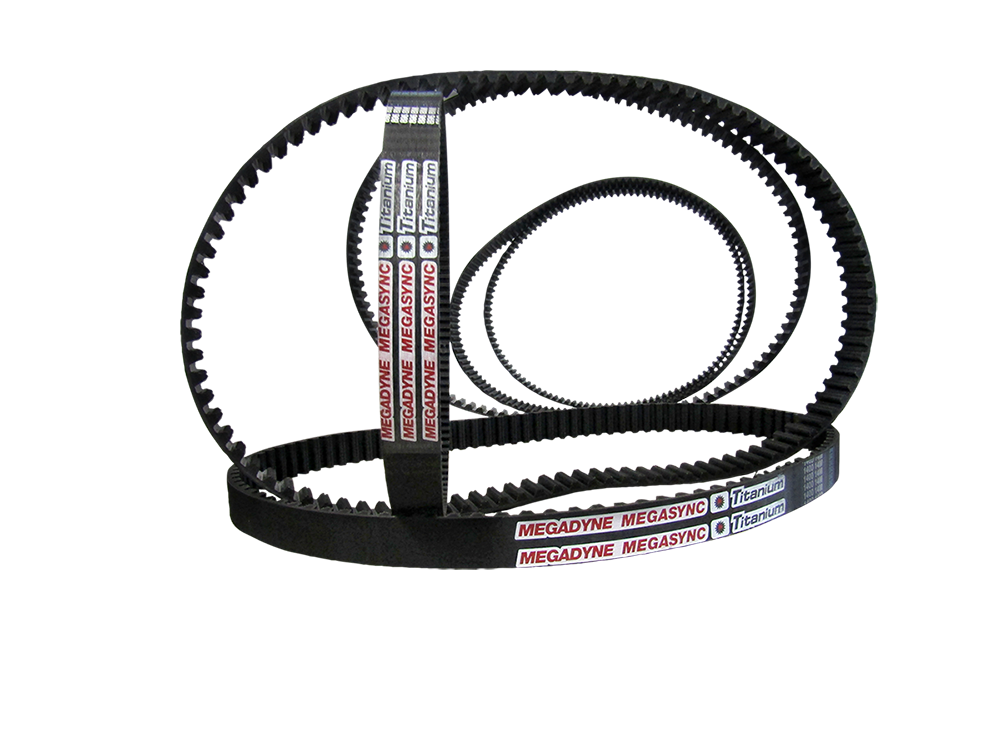
MEGASYNC™ Titanium
Megadyne introduces one of the highest power density synchronous power transmission belt on the market!
Next generation of synchronous belts surpassing the Platinum and other premium belt drives on the market today.
When you want to replace chains, gears or you need to provide a superior belt drive solution - you need MEGADYNE MEGASYNC™ TITANIUM.
With an enhanced design and innovative materials, Titanium has all the features and performance to make it the ideal belting solution in the most demanding applications.
Features
SUPERIOR POWER CAPACITY WITH A MORE COMPACT DRIVE SYSTEM
Main components
BELT BODY
HNBR Elastomer uniquely cross-linked to increase tooth rigidity & durability.
- Superior resistance to flex fatigue
- Expanded range of working temperatures from -40°C (-40°F) to +120°C (+248°F) and ability to withstand peaks up to +140°C (+284°F)
- Highly resistant to mineral oils and abrasion
CORDS
100% carbon, the cord provides extreme dimensional stability (no stretch) under static and dynamic operational loads.
- Maintenance-free, no need to re-tension
- Dual spiral S & Z twist cord provides neutral tracking
- Extremely accurate tooth meshing resulting in the reduction of abrasion, vibrations, & noise
TOOTH FACING FABRIC
High-performing special fabric bonded to the tooth surface.
- Improved torque carrying capacity and tooth shear resistance
- Special film provides self-lubricating properties
- Long lasting durability and antistatic properties
- Low friction, increased drive efficiency with less sprocket wear
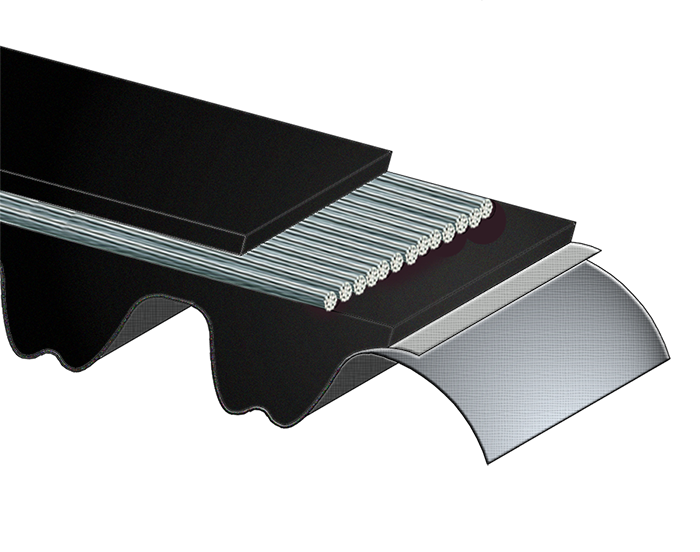
Mechanical and chemical properties
- Lower noise and less weight than roller chain, gears or even polyurethane belts.
- Does not require lubrication nor frequent re-tensioning.
- On average lasts 3-4 times longer than roller chain; if already replacing roller chain once a year, it could be possible to extend maintenance interval to once every 3 years.