When you’re designing or modernising your traction system, you must make an important decision. Should you use belts or ropes? In the article below, we’ll show you the advantages of using traction belts over traditional steel ropes.
1. Longer lifetime
Traction belts have a much longer service life in comparison with ropes. Their lifetime may reach up to 15 years, as in the case of P3.3. How is this possible? While in ropes steel cords are exposed to external factors, in belts they are encapsulated within their structure. That way the cords are protected against various environmental factors (like moisture or UV rays), chemicals, and rust.
In ropes, the cords are exposed, causing vibrations and extensive wear. Metal-to-metal contact is inevitable. The opposite is true for belts. Steel cords hidden inside the construction make the belt resistant to abrasion.
Also, the belts have much smaller diameter cords than the ropes. They allow more flexibility and, therefore, more fatigue resistance.
2. More usable space
Rope traction systems require large sheaves with an extra machine room and large cabin rollers. Their construction requires additional space, which is not the case in traction systems using belts. Belts enable smaller sheaves and pulley diameters, which fit into the shaft together with a controller. As a result, you get a true machine-room-less construction with a much smaller headroom. There’s more usable space at your disposal! If the elevator can reach the last floor, the market value of that floor is increased. But space efficiency is not the only benefit of belts. You also avoid the costs, time and effort associated with building a machine room.
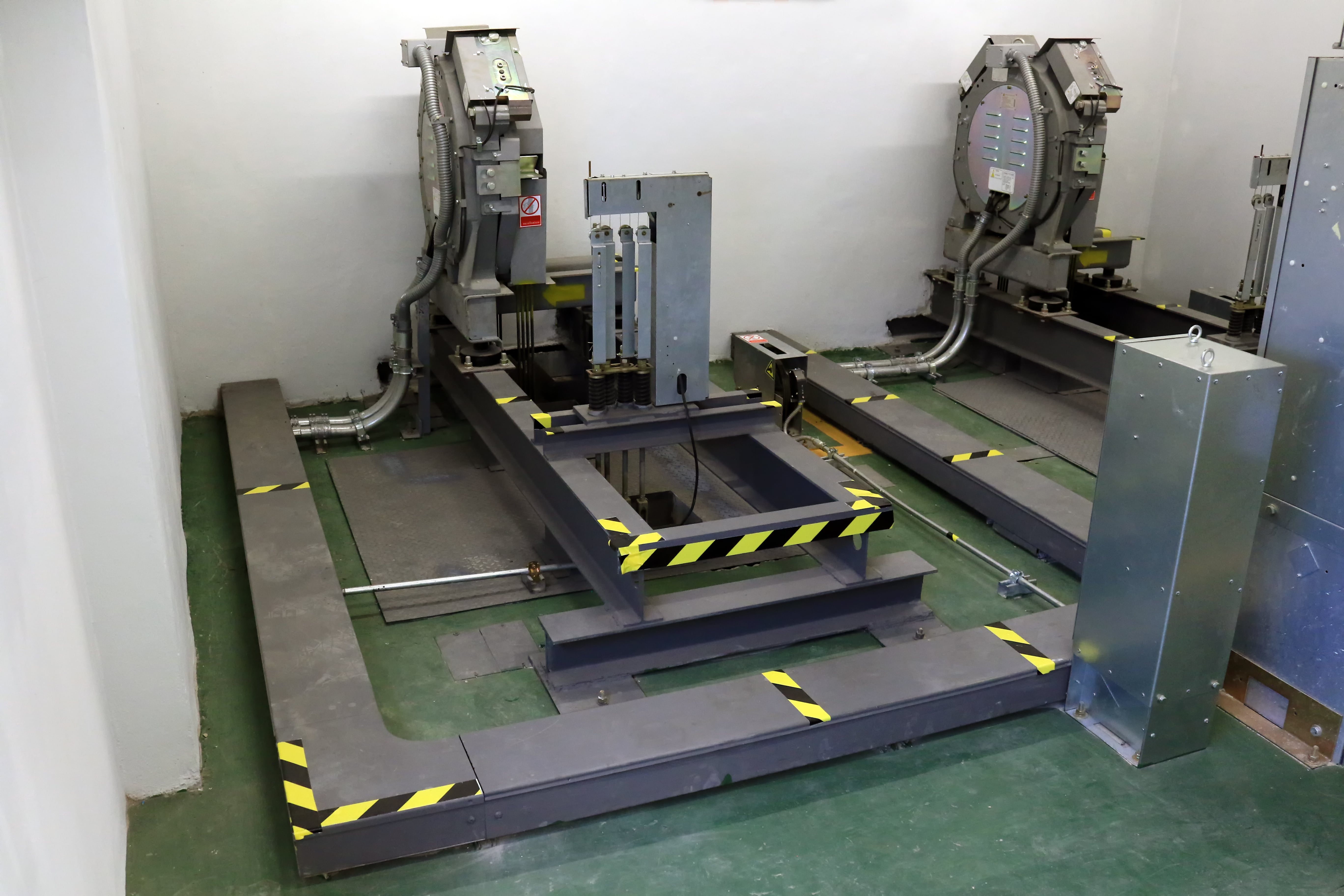
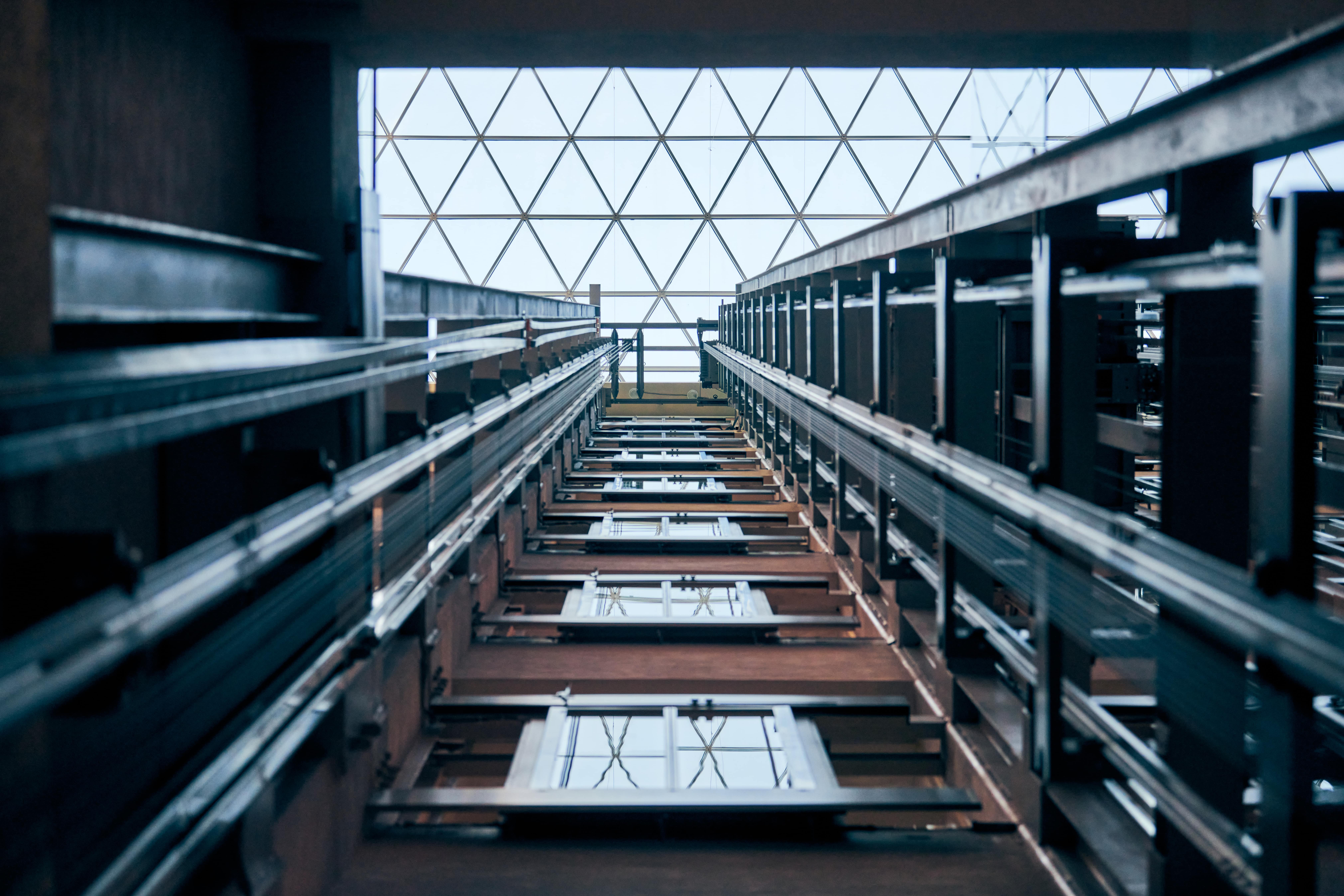
3. Energy efficiency
Polyurethane belts are more energy efficient than steel ropes as they require smaller pulley diameters and less power to move the same load. They also reduce the torque enabling smaller gearless motors. The elimination of a gearbox means energy savings can reach even 35%. That’s a huge difference! You obtain a true gearless system and avoid losses. Ropes, on the contrary, require large pulleys, which consume much more energy.
By optimising your traction system with belts instead of ropes, you can reduce energy costs and ensure that your performance is more sustainable. The technology is more eco-friendly and leaves a lower energy footprint.
4. Lower noise
Coated steel belts eliminate the noise created by the metal-to-metal contact typical for conventional ropes. They enable the use of gearless motors resulting in the reduction of vibration and noise inside and outside the cabin. You and your clients get quiet operation.
5. Smooth ride
Upgrading a traction system with belts ensures a comfortable and smooth ride. Belts permit gearless machines, which don’t shake due to gear engagement and rope vibration. There are no rough stops and starts, which are so characteristic of steel ropes.
6. Reduced costs and maintenance
Another argument in favour of belts is the reduction of costs and maintenance. Belts have longer service lifetimes and, as a result, require less frequent replacements compared with ropes. Moreover, you save a lot of money because you no longer need to build a costly machine room and you don’t overspend on energy consumption.
Maintenance of a traction system with belts is also much more convenient and cheaper. Why? Because belts don’t require lubrication. They run grease-free on the pulleys, which significantly lowers maintenance costs and time. You don’t use gear oil, so there is no need for an oil change, storage, cleanup, and disposal of hazardous waste.
Contact us
Using belts instead of traditional steel ropes is the best way to optimise your traction system in terms of:
- service lifetime,
- space,
- energy efficiency,
- noise,
- smoothness of the ride,
- costs and maintenance.
If you’re willing to give it a try, contact us. We’ll be happy to make your business move.