At Megadyne, we have a reputation for going beyond what is expected to meet the quality requirements and delivery expectations of our OEM customers.
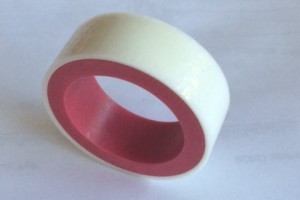
Custom-made solutions for our clients
One customer, a manufacturer of mass transit fare card reading equipment and pre-paid parking ticket dispensers, approached us to produce a silicone feed tire they had been purchasing from another supplier. The supplier was not meeting the OEM’s expectations in terms of lead times and delivery. Since they had worked with us in the past, they were confident we could meet delivery targets that aligned with their production flow.
Megadyne was supplied with a sample, a CAD drawing, as well as material specifications. Production of this feed tire was extremely labour-intensive and somewhat challenging due to its small size and narrow dimensions of 1.00” ID x 0.50” in width x 0.25” in thickness. In addition, it required a two-step manufacturing process that added to the complexity.
How did we approach the problem?
Megadyne assembled an in-house product development team to review and plan the best way to manufacture the feed tire in a timelier manner while maintaining the quality and integrity of the product. Materials specialists spent weeks in our R&D lab formulating the compounds, while manufacturing specialists engineered the two-stage process that involved:
- Applying an internal liner of cured ground urethane over a mandrel
- Applying a silicone top coat with a high gloss finish. This high gloss finish was necessary to enable the smooth travel of the cards through the reading and dispensing mechanisms.
Using a custom-engineered equipment configuration, Megadyne fabricated these small tires accurately at fast cycle times. Quality control inspections including dimensional measurements of length, width, outer diameter, and inner diameter validated that we upheld close tolerances of ± .001”. Our fresh approach to production allowed us to ship quality products within the time constraints needed by our client.
The feed tire manufactured by Megadyne now provides reliable card capture and return performance for the mass transit fare collection system and has proven to keep up with the fast pace of busy commuters and travellers. We continue to manufacture these feed tires that work as well, if not better, than the original, at the rate of 2,000-3,000 units annually. To learn more about our expert belt manufacturing capabilities, contact us today.
Technical parameters
Product Description - Silicone Feed Tire for Mass Transit Fare Collection and Dispensing Equipment
Capabilities Applied/Processes:
Multiple Compounds
Two-stage manufacturing process consisting of:
- Cured ground urethane over a mandrel
- Silicone Top Coat with a high gloss
Overall Part Dimensions
- Thickness – .25″
- ID – 1″
- Width – .5″
Tightest Tolerances - ± .001″
Material Used
- Urethane
- Silicone
Material Finish - High Gloss
Industry for Use - Mass Transit (Fare Collection)
Volume - 2,000 – 3,000 per year
Delivery/Turnaround Time - 6 Weeks